Four techniques for quality assurance of chamfering pipe cutting
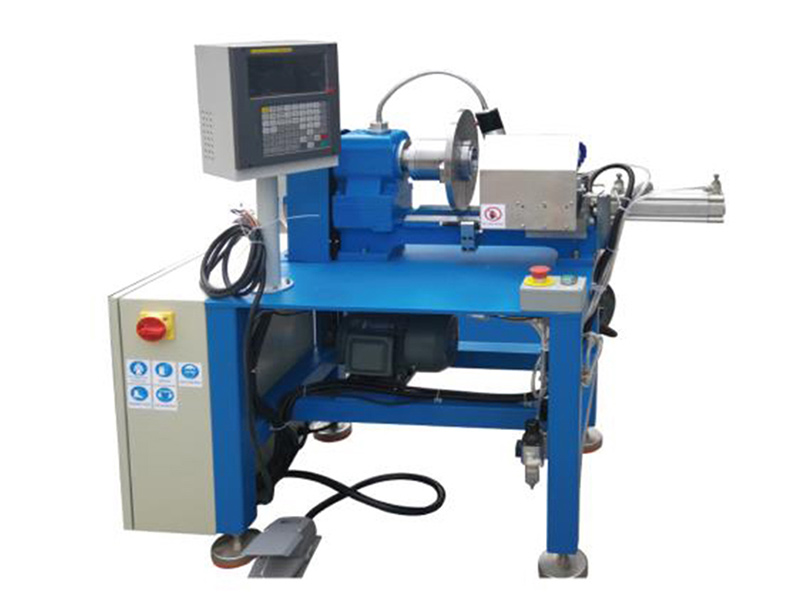
Suzhou Industrial Park Maite Automation Technology Co., Ltd. has been engaged in the R & D and manufacturing of gasket related equipment for 10 years, and now has a full range of metal gasket production equipment, including metal wound gasket, corrugated gasket and other related machinery and equipment.
News Detail
Chamfering machine chamfering speed is too fast, too slow, is not conducive to ensure the quality of the incision. Too fast chamfering speed of chamfering machine may lead to uncut phenomenon. If the chamfering speed of chamfering machine is too slow, it will not only cause waste, but also make the top of the incision melt together, so it is necessary to chamfer the chamfering machine twice. The nozzle model can be selected according to the thickness of the plate. The larger the number of cutting nozzles, the thicker the steel plate thickness of chamfering machine. The distance between the cutting nozzle and the steel plate should be in the same plane. If the cutting nozzle is too close to the steel plate, it is easy to block the cutting nozzle. If the cutting nozzle is too far away, the preheating area of the steel plate will be increased, the deformation will be increased, and the chamfering speed of the chamfering machine will be reduced.

1.3 reasonable chamfering program of chamfering machine NC chamfering machine chamfering machine is controlled by computer in real time to complete chamfering of automatic chamfering machine. What it identifies is the program, so the parts are on the steel plate
The method of programming in this paper plays a decisive role in the machining quality of chamfering parts of chamfering machine.
1.3.1 influence of chamfering sequence of chamfering machine chamfering sequence of chamfering machine refers to the sequence of chamfering machine chamfering several nested nesting parts on steel plate. Generally, the principle of "first inside then outside, first small then large" should be followed, that is, first chamfering the internal contour hole or nested parts in the internal contour of the cutting piece, then chamfering the external contour of the chamfering machine, first chamfering the parts with small area, and then chamfering the parts with large size. Otherwise, chamfering the internal contour or other parts of the chamfering machine on the steel plate which is separated from the motherboard and cannot maintain reliable positioning by self weight Small parts can cause further deformation, resulting in scrap.
1.3.2 influence of chamfering direction of chamfering machine the correct chamfering direction of chamfering machine should ensure that most of the last cutting edge is separated from the motherboard. If it is separated from the motherboard too early, the surrounding corner frame is not enough to resist the thermal deformation stress in the chamfering process of chamfering machine, resulting in the displacement of chamfering parts of chamfering machine in the chamfering process of chamfering machine.
1.3.3 selection of fire point in general, the fire point of chamfered parts of chamfering machine is the best in the middle of the slit of chamfered parts of chamfering machine outside the edge of steel plate. If the distance is too small, the cut parts will be damaged and waste products will appear.
1.3.4 the most ideal way to select the cutting method is to introduce the circular arc, which is gradually approaching along the tangent direction of the chamfering edge of the chamfering machine, so as to realize the smooth transition of the cutting section. The straight line leading in is along the normal direction of the cutting edge, and the crater will appear at the leading in position, which will affect the appearance of the cutting edge, and even cause waste products.
2 control of chamfering quality of chamfering machine for various thickness plates. Different chamfering speed, chamfering gas pressure and cutting nozzle type should be adopted for different thickness plates
When the chamfering machine starts chamfering parts, it is not necessary to cut from the edge of the steel plate, but to use the perforation method to make the edge of the steel plate closed, and there is a certain distance between the edge of the steel plate and the edge of the steel plate, which can limit the size deviation of parts caused by deformation; For 20-100 thick plate, because the chamfering machine is not easy to deform when chamfering, and the piercing operation is severe, it is easy to block the cutting nozzle. It can be cut from the edge of the steel plate. The quality problem of insufficient perpendicularity of the chamfering surface of the chamfering machine often exists in the NC automatic gas cutting of thick plate. Therefore, before chamfering the thick plate chamfering machine, it should try to cut two transverse and longitudinal incisions, and use the straight cutting tool The perpendicularity of two directions of the cutting torch is detected and adjusted by the angle ruler to make the chamfering surface of the chamfering machine perpendicular to the surface of the steel plate.
3. Quality control of chamfering machine for parts with holes when chamfering parts with holes, chamfering machine should be used to chamfering the inner hole of parts first, and then chamfering machine should be used to chamfering the periphery of parts, so as to ensure the dimensional accuracy of inner hole and periphery. In addition, the diameter of the inner hole can be further reduced, and the plate thickness can be appropriately increased. In order to reduce the preheating time, the preheating oxygen should be appropriately increased (especially for medium and heavy plate), the reasonable piercing point should be selected, and the change of preheating position of steel plate should be observed. When the chamfering temperature of chamfering machine (i.e. the ignition point) is reached, the chamfering oxygen control valve of chamfering machine should be opened, and the speed should be appropriately increased until all the chamfering oxygen control valves of chamfering machine are opened. In the process of piercing, attention should be paid to adjusting the speed and oxygen control valve to make the slag fly out approximately 40 degrees with the cutting nozzle. When the diameter of the inner hole is less than the thickness of the plate, it is not suitable to drill the chamfering machine for chamfering, and the hole diameter should be machined; when the thickness of the plate is more than 120mm, it is also not suitable to drill the chamfering machine for chamfering. If the diameter of the inner hole is larger, a chamfering hole with a diameter of 20mm can be drilled in the corresponding position by machining method, and then the inner hole chamfering machine can be chamfered.
4 quality control of chamfering machine for long and thin parts (i.e. parts with large ratio of length and width) when chamfering machine according to conventional methods, due to the deformation of steel plate due to heating, there will be camber and warpage, and the cutting nozzle will be touched if the operation is not paid attention to, which will affect the smooth chamfering of chamfering machine. It is easy to cause accidents such as flameout, bending and cutting torch breaking. Therefore, local water spray cooling can be used; bridge chamfering machine chamfering, that is, manually leaving several sections of 15-30mm bridge chamfering machine chamfering, so that it is connected with the motherboard through the bridge to contain the cold shrinkage and arch; two cutting torches chamfering machine chamfering both sides of the web at the same time, and finally the transverse chamfering machine chamfering to the required size, which can effectively control the chamfering quality of slender parts .